In the rapidly evolving healthcare landscape, the success of medical devices hinges not just on groundbreaking design, but on the unwavering reliability and performance of their foundational materials and the stability of their supply. The global medical device materials market is projected for significant growth, reaching an estimated $67.32 billion by 2034 with a robust Compound Annual Growth Rate (CAGR) of 13.24% from 2025. This substantial expansion, fueled by increasing demand for minimally invasive procedures, personalized medicine, and the integration of smart technologies, underscores the critical need for robust, trustworthy material partnerships. Medical device manufacturers operate under immense pressure to innovate quickly while adhering to stringent quality and regulatory standards. LG Chem, a leading materials science company, deeply understands these demands and is dedicated to providing comprehensive solutions that ensure reliability, safety, and environmental responsibility, acting as a true "Total Solution Provider" throughout the entire product lifecycle.
Uninterrupted Innovation: The Backbone of LG Chem's Stable Global Supply Chain
For medical device manufacturers, consistent access to high-quality materials is non-negotiable, directly impacting production schedules, market availability, and ultimately, patient care. LG Chem's commitment to supply stability is built on three foundational pillars: Dedicated Production Lines, Unwavering Quality Control, and a Robust Supply Chain Management System. This comprehensive approach addresses the anxieties and strategic needs of manufacturers seeking operational continuity and peace of mind in a dynamic, high-stakes market.
LG Chem operates dedicated production lines specifically for medical device materials, ensuring a seamless and uninterrupted supply that meets the most stringent quality and safety standards in the industry. This commitment extends to guaranteeing continuous production with no planned shutdowns for 12 months. This proactive stance, coupled with rigorous testing and quality control processes, effectively eliminates sudden shortages and empowers manufacturers to manage inventory efficiently and scale production with unwavering confidence. The inherent reduction in material or process changes on dedicated lines significantly reduces the likelihood of costly re-validation procedures and potential regulatory hurdles for device manufacturers.
A cornerstone of LG Chem's supply stability and a critical differentiator is the 12-month Notification of Change (NOC) program. This program provides medical device manufacturers with ample lead time for any potential material or process changes, offering maximum planning flexibility. This directly supports the objective of minimizing any change in production and ensuring stable quality. The NOC program provides a critical buffer, allowing manufacturers to proactively plan, test, and adapt their own processes without disrupting production or jeopardizing regulatory compliance. This translates directly into reduced operational risk, lower compliance costs, and improved time-to-market for LG Chem's customers.
With manufacturing operations strategically based in Yeosu, Korea, and established warehouse networks, LG Chem ensures reliable global response, with typical lead times to US/Europe ranging from 8-10 weeks. This global footprint, combined with "no restrictions within Capa," signifies a robust capacity to meet diverse customer needs worldwide, ensuring on-time delivery and flexible response. The holistic integration of dedicated lines, the NOC program, and global logistics signifies a strategic investment by LG Chem to differentiate itself not just on material properties, but on the reliability and predictability of its entire supply chain ecosystem. In a globalized medical device market, supply chain resilience is a competitive advantage, fostering deep trust and strengthening long-term collaborative relationships.
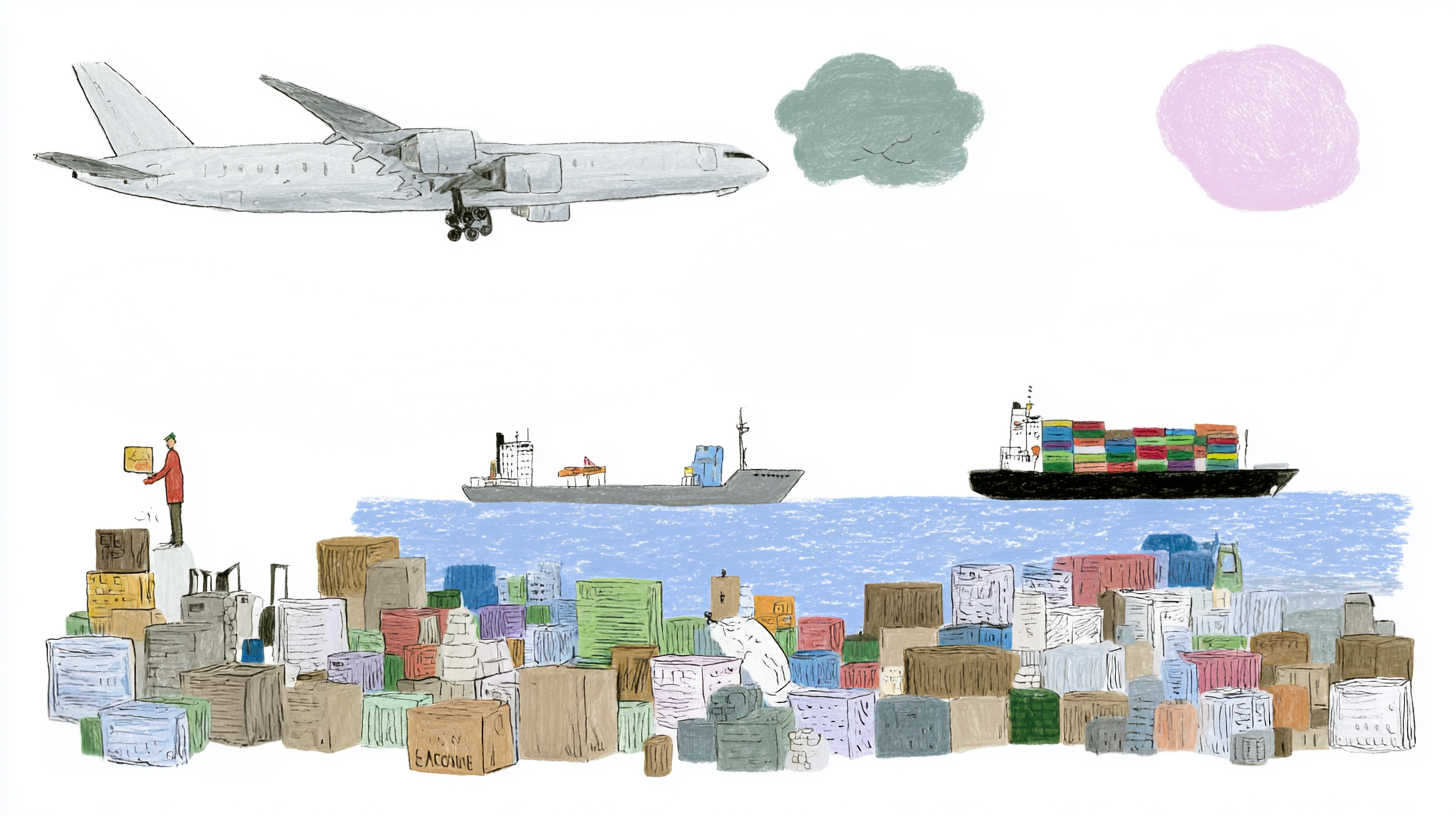
The Power of Polycarbonate: LG Chem's Advanced PC for Medical Applications
Polycarbonate (PC) is a high-performance engineering plastic widely adopted in medical devices due to its exceptional transparency, high strength, excellent heat and impact resistance, superior biocompatibility, and excellent dimensional stability. These properties make it an ideal choice for critical applications where clarity, durability, and safety are paramount. While Acrylonitrile Butadiene Styrene (ABS) offers good mechanical strength and chemical resistance, PC provides distinct advantages, particularly in applications demanding superior transparency, higher heat resistance, and greater impact resistance. For instance, in devices requiring visual clarity or repeated sterilization cycles, PC's robust mechanical integrity and optical properties are often preferred.
LG Chem's PC2080-20 grade is specifically engineered for gamma sterilization compatibility. This is a crucial feature, as gamma irradiation is a common and highly effective sterilization method for many medical devices. Gamma sterilization, while effective, can induce polymer degradation, leading to issues like discoloration, embrittlement, or loss of mechanical strength in conventional plastics. For medical devices, such degradation can compromise device safety, efficacy, and regulatory compliance. PC2080-20 is designed to provide a good balance of physical and mechanical properties even after exposure to gamma radiation, ensuring the integrity and consistent performance of the device throughout its intended lifecycle. This specialized grade is also produced under a dedicated production line to provide more stable quality and to minimize any change in production. This engineering achievement directly addresses a critical industry challenge, reducing the need for extensive and costly post-sterilization validation by manufacturers, and ultimately, enhancing patient safety by guaranteeing device integrity.
LG Chem's PC materials are utilized across a diverse range of medical applications, including Luer locks, LED masks, and renal devices such as dialyzer housings. These examples highlight PC's adaptability and proven performance in demanding healthcare environments.
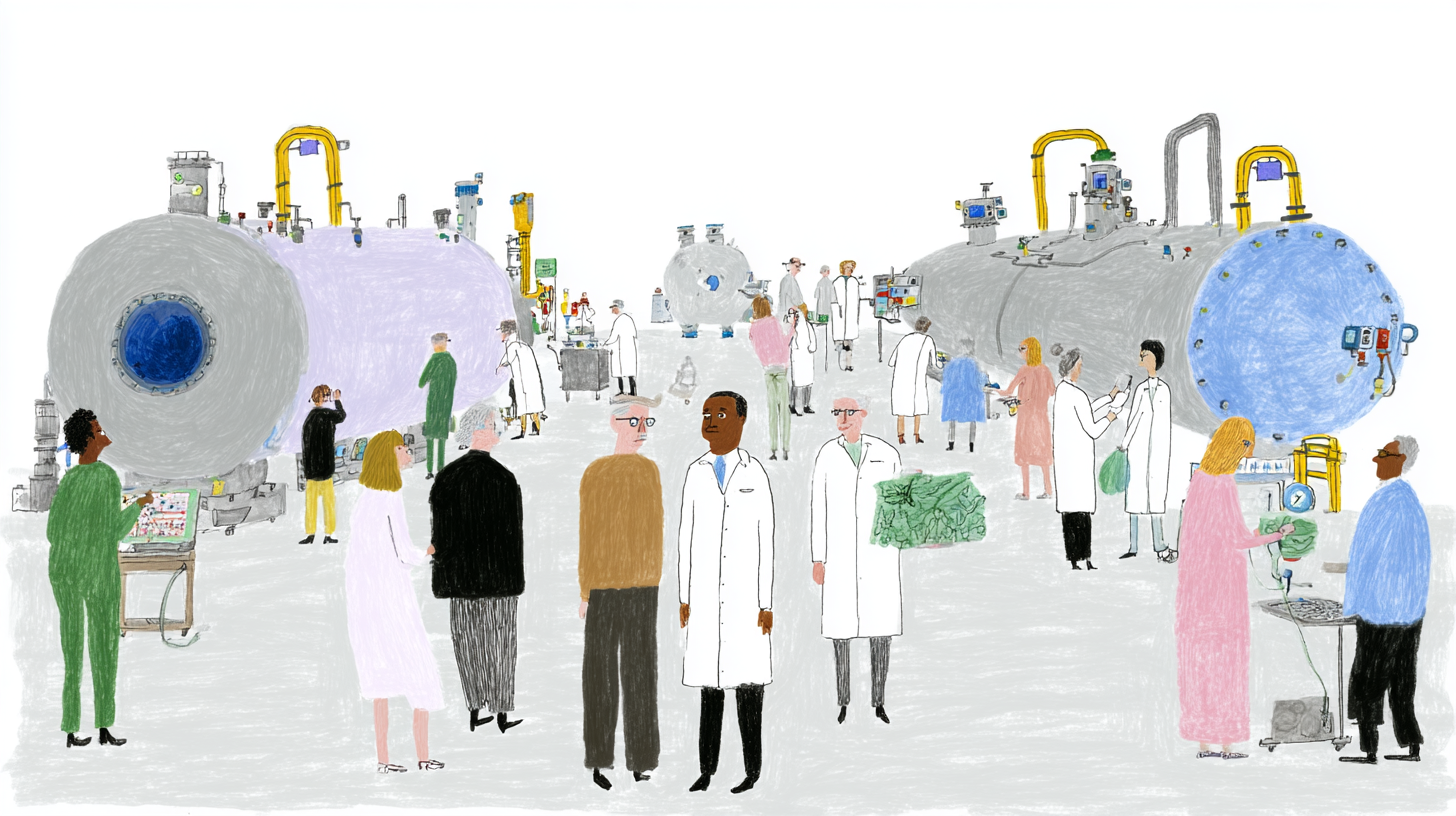
Compliance and Confidence: Navigating Regulatory Landscapes with a Total Solution Partner
In the medical device sector, stringent regulatory compliance is non-negotiable. LG Chem's materials are engineered to meet and exceed critical global standards, including ISO 10993 (evaluating biocompatibility, covering cytotoxicity, sensitization, and irritation), USP Class VI (confirming material safety through rigorous biological testing as defined by the U.S. Pharmacopeia), and FDA (certifying that the material or device meets safety and performance requirements for market approval). Specifically, PC2080-20 is certified to ISO 10993-3, 4, 5, 6, 10, 11, demonstrating comprehensive biocompatibility testing for its intended applications.
This comprehensive suite of certifications, combined with the strategic 12-month Notification of Change (NOC) program, collectively provides a significant competitive advantage by substantially de-risking the material selection, qualification, and ongoing regulatory compliance processes for manufacturers. For medical device companies, achieving and maintaining regulatory approval is a monumental, resource-intensive task. Sourcing pre-certified materials significantly reduces the burden of in-house testing, documentation, and the overall time-to-market. The NOC program further mitigates the risk of unexpected material changes that could jeopardize existing regulatory approvals or force expensive re-submissions. This allows LG Chem's customers to allocate more resources to core innovation and product development, rather than being encumbered by compliance hurdles.
As a true "Total Solution Provider," LG Chem offers comprehensive global technical support through its dedicated customer solution center. This includes invaluable assistance with injection molding and processing guidance, detailed sample testing, and expert support throughout the entire manufacturing process. Furthermore, LG Chem's diverse portfolio allows for extensive customization to meet highly specific requirements for enhanced durability, flexibility, or biocompatibility, ensuring tailored solutions for unique medical device designs. This collaborative approach transforms LG Chem from a mere material supplier into a strategic R&D and manufacturing partner for its clients, fostering faster innovation, more efficient problem-solving, and ultimately leading to superior end products and stronger, more enduring customer relationships.
Real-World Impact: Proven Applications of LG Chem's PC Materials
LG Chem's PC materials have demonstrated their efficacy and versatility in various real-world applications. For instance, PC2001-10 and PC2001-20 grades have been successfully implemented by Company S, a U.S.-based premium home appliance company, for their advanced LED Masks. This application leverages PC's excellent transparency, heat resistance, and durability, which are crucial for consumer-facing medical aesthetic devices requiring consistent performance and aesthetic appeal.
In another significant case, LG Chem's PC (PC2001-10) was adopted by Company T, a prominent medical device manufacturer based in China, specializing in disposable infusion products, pressure pumps, and T-type connectors. In this critical application, PC's high strength, chemical resistance, and exceptional dimensional stability are paramount for ensuring the safety, reliability, and leak-proof integrity of fluid delivery systems. These examples serve as tangible proof points, demonstrating the versatility and real-world validation of LG Chem's PC materials across different medical device categories and diverse geographical markets. Seeing that LG Chem's materials have been successfully integrated into commercial products by other reputable companies significantly builds credibility and reduces the perceived risk associated with adopting new materials.
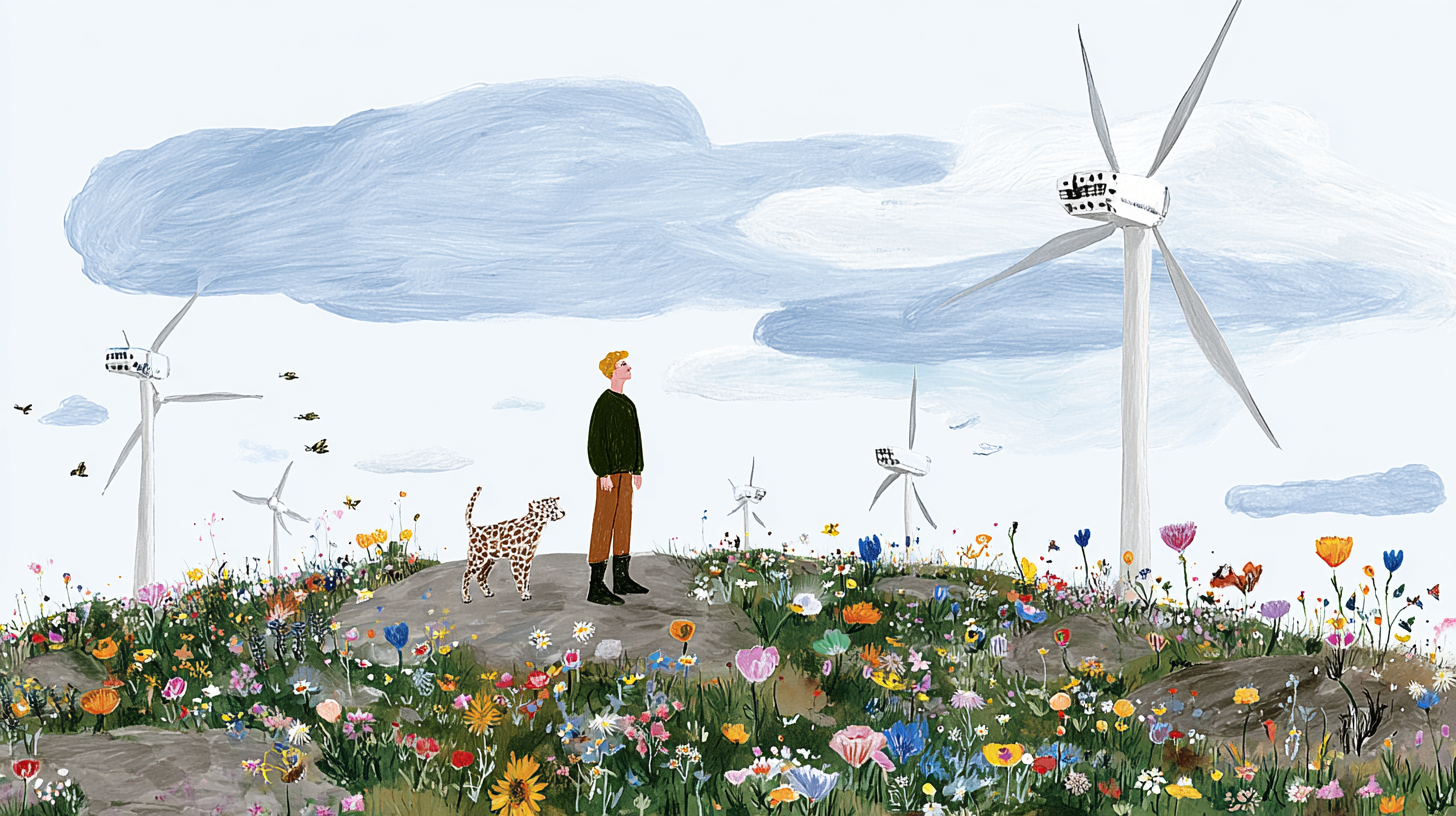
Driving a Sustainable Future in Healthcare
The medical device industry is increasingly recognizing its environmental footprint and the urgent need for more eco-friendly solutions. Market forecasts indicate a substantial increase in the adoption of sustainable materials over the next decade, driven by rising awareness and regulatory pressures. LG Chem is at the forefront of this critical sustainability transition with its dedicated LETZero brand, offering a robust portfolio of eco-friendly materials. This includes recycled (made of reprocessed waste plastics), bio-based (made of renewable materials), and compostable materials (decomposed within six months to two years under specific conditions). These materials are rigorously tested to ensure they meet the same high standards for quality and reliability, allowing manufacturers to transition to sustainable solutions without compromising performance or safety.
LG Chem's deep commitment to sustainability is further validated by a series of prestigious certifications, including UL ECV (verifies environmental claims), TÜV SÜD (evaluates quality, safety, performance), GRS (Global Recycled Standard, verifies recycled content and social responsibility), and ISCC Plus (ensures sustainability and traceability of bio-based/circular raw materials). These certifications provide independent assurance that LG Chem's materials meet global environmental standards, actively supporting customers in achieving their own sustainability goals. LG Chem's proactive investment in sustainability through its LETZero portfolio and comprehensive environmental certifications positions them as a forward-thinking, future-proof partner, aligning with evolving industry values and anticipating potential future regulations. This can attract environmentally conscious partners, enhance brand reputation, and future-proof their business against stricter environmental regulations, adding another significant layer of long-term value.
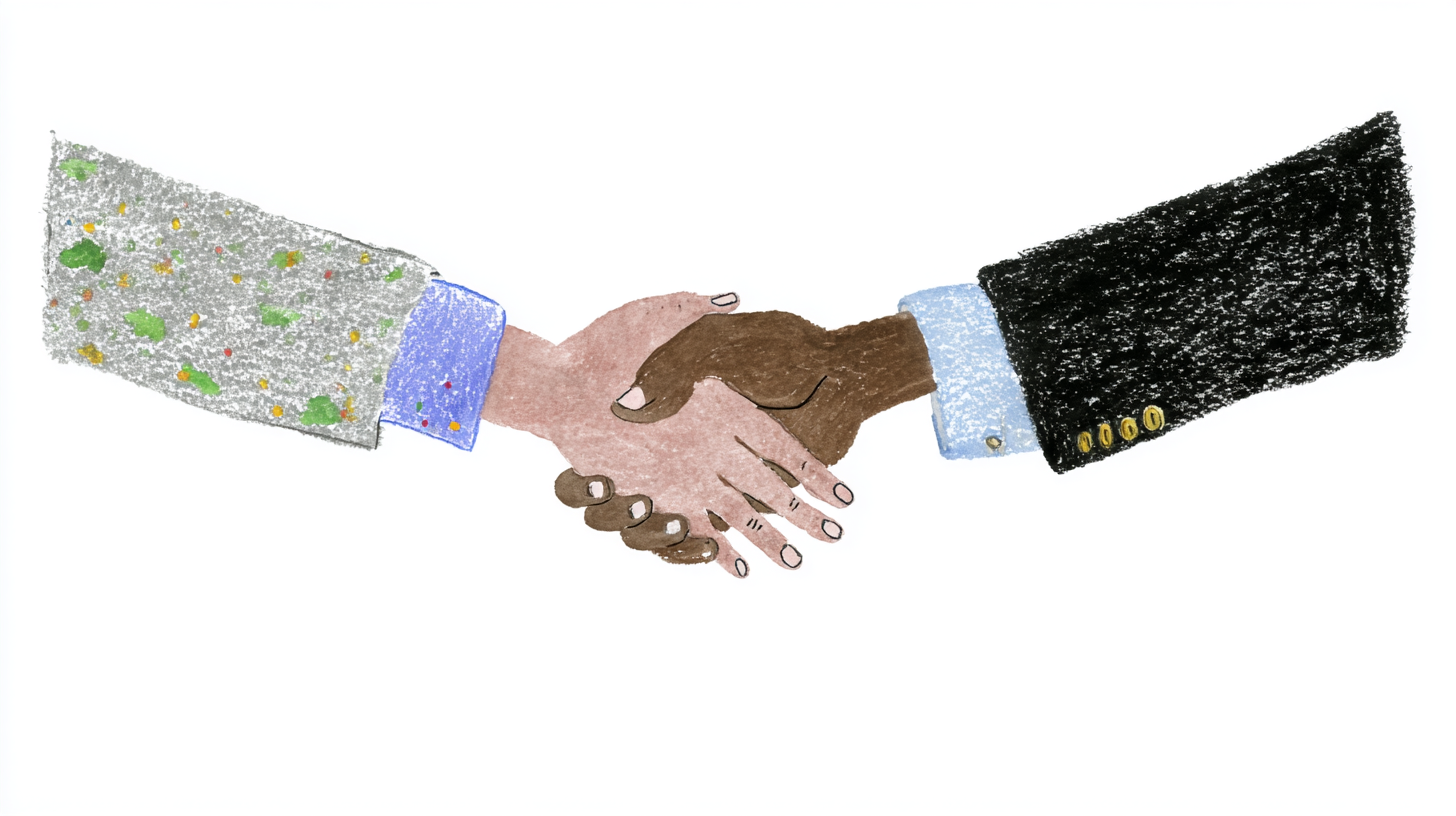
Partnering for a Healthier Tomorrow
In an industry where precision, reliability, and innovation are paramount, LG Chem stands as a trusted, indispensable partner for medical device manufacturers. The unwavering commitment to supply stability, exemplified by dedicated production lines, robust quality control, and the unique 12-month NOC program, ensures uninterrupted access to high-performance materials critical for patient care.
LG Chem's advanced Polycarbonate grades, particularly the gamma sterile PC2080-20, offer a superior balance of physical and mechanical properties, coupled with full regulatory compliance, empowering the development of safer, more effective medical devices that withstand the rigors of sterilization. As a true total solution provider, LG Chem offers comprehensive technical support and a diverse, customizable material portfolio, further enhanced by a proactive dedication to sustainability through the LETZero brand.
Explore how LG Chem's innovative medical device materials and unparalleled support can elevate your next project and contribute to a healthier tomorrow. Contact LG Chem today to discuss specific needs and download Technical Data Sheets for detailed material specifications.